What Are the Raw Materials for Gloves?
Table of Contents
- Introduction
- Primary Raw Materials Used in Glove Manufacturing
- Essential Role of Gloves Machine Manufacturer in Material Selection
- Specialized Raw Materials for Different Glove Types
- How Gloves Machine Manufacturer Influences Material Processing
- Quality Standards and Material Testing
- Conclusion
Introduction
The glove manufacturing industry relies on a diverse range of raw materials to produce protective handwear for medical, industrial, and consumer applications. Understanding these materials is crucial for manufacturers, suppliers, and end-users who depend on high-quality gloves for safety and performance. From natural rubber latex to advanced synthetic compounds, each material brings unique properties that determine the final product’s characteristics, durability, and suitability for specific applications.
Primary Raw Materials Used in Glove Manufacturing
Natural Rubber Latex
Natural rubber latex remains one of the most important raw materials in glove production. Extracted from the Hevea brasiliensis tree, this material provides excellent elasticity, comfort, and barrier protection. The latex undergoes several processing stages, including concentration, stabilization, and vulcanization, to achieve the desired properties for glove manufacturing.
The quality of natural rubber latex significantly impacts the final product’s performance. Premium-grade latex ensures better tensile strength, puncture resistance, and overall durability. However, concerns about latex allergies have led many manufacturers to explore alternative materials while maintaining the superior protective qualities that latex provides.
Synthetic Materials
Synthetic materials have revolutionized the glove industry by offering latex-free alternatives without compromising protection levels. Nitrile rubber, derived from acrylonitrile and butadiene, provides excellent chemical resistance and durability. This material is particularly popular in medical and industrial applications where exposure to oils, chemicals, and bodily fluids is common.
Vinyl, made from polyvinyl chloride (PVC), offers a cost-effective solution for light-duty applications. While not as durable as nitrile or latex, vinyl gloves provide adequate protection for food service and general-purpose tasks. Polyethylene represents another synthetic option, primarily used for disposable gloves in food handling and light industrial work.
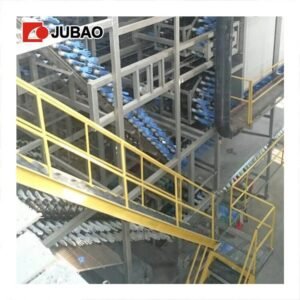
Fabric and Textile Materials
Fabric-based gloves incorporate various textile materials to provide comfort, breathability, and specialized protection. Cotton serves as a foundational material for many work gloves, offering comfort and moisture absorption. Polyester blends enhance durability and reduce shrinkage, while nylon adds strength and abrasion resistance.
Advanced textile materials include aramid fibers for heat resistance, ultra-high molecular weight polyethylene for cut protection, and specialized coatings that enhance grip and chemical resistance. These materials are often combined in multi-layer constructions to achieve specific performance characteristics.
Essential Role of Gloves Machine Manufacturer in Material Selection
Machine Compatibility Requirements
A reputable gloves machine manufacturer plays a crucial role in determining which raw materials can be effectively processed. Different manufacturing equipment requires specific material properties to ensure optimal production efficiency and product quality. The viscosity, temperature sensitivity, and chemical composition of raw materials must align with the machine’s capabilities.
Modern glove manufacturing equipment is designed to handle multiple material types, but each requires specific processing parameters. Temperature control systems, mixing mechanisms, and curing processes must be calibrated according to the chosen raw material. This compatibility ensures consistent product quality and minimizes production waste.
Quality Control Standards
Professional gloves machine manufacturer companies implement stringent quality control measures that directly influence raw material specifications. These standards ensure that materials meet international safety requirements and performance benchmarks. Regular testing protocols verify material consistency, contamination levels, and chemical composition.
The integration of automated quality control systems allows manufacturers to monitor material properties throughout the production process. This real-time monitoring capability enables immediate adjustments to maintain product quality and reduces the risk of defective products reaching the market.
Specialized Raw Materials for Different Glove Types
Medical Grade Materials
Medical gloves require materials that meet strict biocompatibility standards and provide reliable barrier protection. These materials undergo rigorous testing to ensure they are free from harmful chemicals and allergens. Medical-grade latex, nitrile, and vinyl must comply with FDA regulations and international medical device standards.
Powder-free formulations have become increasingly important in medical applications to reduce the risk of allergic reactions and contamination. This requirement has led to the development of specialized coating materials and surface treatments that maintain the gloves’ donning characteristics without the use of traditional powders.
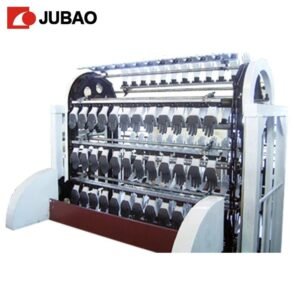
Industrial Protection Materials
Industrial gloves often require specialized materials that provide protection against specific hazards. Chemical-resistant materials include various polymer compounds designed to withstand exposure to acids, bases, solvents, and other industrial chemicals. These materials must maintain their integrity under extreme conditions while providing tactile sensitivity.
Cut-resistant materials incorporate high-performance fibers such as Kevlar, Dyneema, and steel fibers. These materials are engineered to prevent laceration injuries while maintaining flexibility and comfort. The combination of different protective materials in layered constructions provides comprehensive protection against multiple hazards.
Food Service Materials
Food-safe materials must comply with FDA food contact regulations and maintain their properties under various temperature and moisture conditions. These materials cannot impart taste, odor, or harmful substances to food products. Polyethylene, vinyl, and specialized nitrile formulations are commonly used in food service applications.
Temperature resistance is particularly important for food service gloves, as they may be exposed to hot surfaces, steam, and freezing conditions. Materials must maintain their flexibility and barrier properties across a wide temperature range while remaining safe for food contact.
How Gloves Machine Manufacturer Influences Material Processing
Advanced Processing Techniques
Leading gloves machine manufacturer companies continuously develop new processing techniques that expand the range of usable raw materials. Advanced mixing systems ensure uniform material distribution, while precision temperature control enables the processing of temperature-sensitive materials. These technological improvements allow manufacturers to work with innovative materials that were previously difficult to process.
Automation technologies have revolutionized material handling and processing efficiency. Automated material feeding systems reduce contamination risks and ensure consistent material quality throughout production runs. Computer-controlled processing parameters enable precise adjustment of material properties to meet specific performance requirements.
Material Optimization
Modern manufacturing equipment enables the optimization of raw material usage through precise control of material thickness, distribution, and curing processes. This optimization reduces material waste while maintaining product quality and performance standards. Advanced monitoring systems track material consumption and identify opportunities for efficiency improvements.
The development of multi-material processing capabilities allows manufacturers to combine different raw materials in single products. This capability enables the creation of gloves with varying properties across different areas, such as enhanced grip zones, reinforced fingertips, or specialized palm coatings.
Quality Standards and Material Testing
Raw material quality directly impacts the safety and performance of finished gloves. Comprehensive testing protocols evaluate material properties including tensile strength, elongation, puncture resistance, and chemical compatibility. These tests ensure that materials meet industry standards and regulatory requirements.
International standards such as ASTM, EN, and ISO provide guidelines for material testing and quality assessment. Regular testing throughout the production process ensures consistent quality and helps identify potential issues before they affect the final product. Material traceability systems enable manufacturers to track raw material sources and maintain quality records.
Conclusion
The selection and processing of raw materials represent critical factors in glove manufacturing success. From natural rubber latex to advanced synthetic compounds, each material contributes unique properties that determine the final product’s performance and suitability for specific applications. The collaboration between material suppliers and equipment manufacturers ensures that raw materials are processed efficiently and effectively to produce high-quality protective gloves.
Understanding the relationship between raw materials and manufacturing processes enables better decision-making in glove selection and production planning. As technology continues to advance, new materials and processing techniques will further expand the possibilities for creating specialized gloves that meet evolving safety and performance requirements across various industries.