What are the Fillers in Glove Manufacturing?
Table of Contents
- Introduction
- Understanding Fillers in Glove Manufacturing
- Types of Fillers Used in Glove Manufacturing
- Functions and Benefits of Fillers
- Quality Considerations and Standards
- Conclusion
Introduction
Fillers play a crucial role in modern glove production, serving as essential additives that enhance performance while reducing manufacturing costs. These inorganic materials are incorporated into rubber and polymer matrices to improve various properties of protective gloves used across medical, industrial, and consumer applications.
Understanding Fillers in Glove Manufacturing
The glove manufacturing industry relies heavily on fillers to achieve optimal product performance and economic viability. Fillers are typically fine particulate materials that are blended with the primary polymer or rubber compound during the production process. These additives constitute a significant portion of the final glove composition, often ranging from 20% to 60% by weight depending on the specific application requirements.
In glove manufacturing, fillers serve multiple purposes beyond simple cost reduction. They act as reinforcing agents that improve mechanical properties such as tensile strength, tear resistance, and durability. The selection of appropriate fillers depends on factors including the base polymer type, intended use of the gloves, processing conditions, and regulatory requirements.
Types of Fillers Used in Glove Manufacturing
Calcium Carbonate
Calcium carbonate stands as one of the most widely used fillers in glove production. This versatile mineral filler offers excellent cost-effectiveness while providing good reinforcement properties. Ground calcium carbonate (GCC) and precipitated calcium carbonate (PCC) are both utilized, with particle sizes typically ranging from 0.1 to 10 microns. The material enhances stiffness and reduces material costs without significantly compromising flexibility.
Clay Fillers
Various clay minerals, including kaolin and bentonite, serve as effective fillers in glove formulations. These naturally occurring aluminosilicate minerals provide excellent barrier properties and chemical resistance. Clay fillers are particularly valuable in applications requiring enhanced puncture resistance and chemical protection. Their platelet-like structure creates tortuous pathways that improve barrier performance against liquids and gases.
Silica-Based Fillers
Silica fillers, including precipitated silica and fumed silica, offer superior reinforcement capabilities. These materials significantly improve tensile strength and tear resistance while maintaining good processability. Silica fillers are especially important in high-performance glove applications where mechanical properties are critical. The surface area and particle size distribution of silica fillers can be tailored to achieve specific performance characteristics.
Talc
Talc, a hydrated magnesium silicate mineral, serves as both a filler and processing aid in glove manufacturing. Its lamellar crystal structure provides excellent slip properties and helps prevent blocking during storage. Talc fillers contribute to improved surface smoothness and can enhance the release properties of gloves during demolding processes.
Functions and Benefits of Fillers
Cost Reduction
The primary economic benefit of fillers lies in their ability to reduce raw material costs. Since fillers are typically less expensive than the base polymers, their incorporation allows manufacturers to maintain competitive pricing while preserving essential performance characteristics. This cost advantage is particularly important in high-volume production scenarios where material costs significantly impact profitability.
Property Enhancement
Fillers contribute to numerous property improvements in finished gloves. Mechanical reinforcement increases tensile strength, modulus, and tear resistance. Barrier properties are enhanced through the creation of tortuous diffusion pathways. Thermal stability can be improved through the incorporation of thermally stable inorganic fillers. Additionally, certain fillers can provide antimicrobial properties or enhanced chemical resistance.
Processing Improvements
Beyond end-use properties, fillers often improve manufacturing processability. They can reduce compound viscosity, improve mold release, and enhance surface finish quality. Some fillers act as processing aids that facilitate mixing, reduce cycle times, and improve dimensional stability during curing processes.
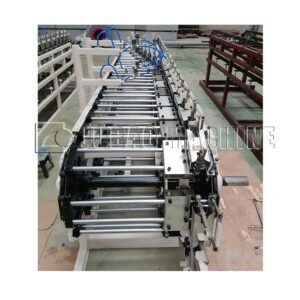
Quality Considerations and Standards
Particle Size Distribution
The particle size and distribution of fillers critically influence both processing characteristics and final product properties. Finer particles generally provide better reinforcement but may increase viscosity and processing difficulty. Optimal particle size selection requires balancing performance requirements with manufacturing constraints.
Chemical Compatibility
Filler compatibility with the base polymer system is essential for achieving consistent properties and avoiding adverse interactions. Surface treatments may be applied to fillers to improve compatibility and dispersion within the polymer matrix. Chemical compatibility testing ensures that fillers do not interfere with curing processes or cause premature degradation.
Regulatory Compliance
Fillers used in medical and food-contact gloves must comply with strict regulatory standards regarding purity, extractables, and biocompatibility. FDA, EU, and other international regulations govern the types and levels of fillers permissible in different glove applications. Comprehensive testing and documentation ensure regulatory compliance throughout the supply chain.
Conclusion
Fillers represent essential components in modern glove manufacturing, providing economic benefits while enhancing product performance. The careful selection and optimization of filler systems enable manufacturers to produce gloves that meet diverse application requirements while maintaining cost competitiveness. As technology advances and regulatory requirements evolve, the development of new filler technologies continues to drive innovation in the glove manufacturing industry.
Understanding the role of fillers empowers manufacturers to make informed decisions about formulation optimization, quality control, and product development. The strategic use of fillers will remain fundamental to the continued growth and advancement of protective glove technologies across all market segments.
Read More: New – JUBAO MACHINE