How to Manufacture Latex Gloves: A Comprehensive Manufacturing Guide
Table of Contents
- Introduction to Latex Glove Manufacturing
- Raw Materials and Quality Control
- Understanding the Latex Gloves Machine Setup
- The Manufacturing Process Step by Step
- Quality Assurance and Testing
- Advanced Latex Gloves Machine Technology
- Production Optimization and Efficiency
- Environmental Considerations
- Conclusion
Introduction to Latex Glove Manufacturing
Latex glove manufacturing is a sophisticated industrial process that combines precise chemistry, advanced machinery, and stringent quality control measures. The production of latex gloves serves critical industries including healthcare, food service, and industrial applications where hand protection is essential.
The manufacturing process involves transforming natural latex rubber into thin, flexible gloves that provide barrier protection while maintaining tactile sensitivity. This complex procedure requires specialized equipment, controlled environments, and adherence to international quality standards such as ASTM and EN specifications.
Understanding the complete manufacturing workflow is crucial for anyone involved in glove production, from plant managers to quality control specialists. This comprehensive guide will walk you through every aspect of latex glove manufacturing, from raw material preparation to final packaging.
Raw Materials and Quality Control
Natural Latex Selection
The foundation of quality latex gloves begins with premium natural rubber latex. Manufacturers typically source latex from rubber plantations in Southeast Asia, where Hevea brasiliensis trees produce the highest quality rubber. The latex concentrate must contain approximately 60% dry rubber content and meet specific viscosity requirements.
Quality control starts at the raw material stage. Each batch of incoming latex undergoes rigorous testing for:
- Total solid content
- Volatile fatty acid numbers
- Mechanical stability time
- pH levels
- Ammonia content
Chemical Additives and Compounding
The latex compounding process involves adding various chemicals to enhance the final product’s properties. Essential additives include:
Accelerators: Zinc diethyldithiocarbamate and zinc mercaptobenzothiazole speed up the vulcanization process.
Antioxidants: Prevent degradation during storage and use.
Surfactants: Improve wetting properties and reduce surface tension.
Coagulants: Calcium nitrate or aluminum nitrate facilitate proper gel formation on the formers.
The compounding process requires precise measurement and thorough mixing to ensure uniform distribution of all additives throughout the latex compound.
Understanding the Latex Gloves Machine Setup
Former Cleaning and Preparation
The manufacturing process begins with thorough cleaning of aluminum hand-shaped formers. These formers are first washed in hot water and detergent to remove any residual materials from previous production runs. Following the initial wash, formers undergo an acid treatment to ensure proper surface preparation.
The cleaned formers then receive a coagulant dip, typically in a calcium nitrate solution at 15-20% concentration. This coagulant layer is crucial for proper latex adhesion during the dipping process. Temperature control during this stage is critical, with coagulant solutions maintained between 60-70°C.
Dipping Line Configuration
Modern latex glove production lines feature automated conveyor systems that carry formers through various processing stations. The typical line includes:
- Pre-heat ovens (100-120°C)
- Coagulant dipping tanks
- Latex dipping tanks with controlled temperature and pH
- Leaching tanks for protein removal
- Vulcanization ovens (100-130°C)
- Stripping stations
Temperature and Humidity Control
Environmental conditions play a crucial role in successful latex glove manufacturing. Production facilities maintain ambient temperatures between 25-30°C with relative humidity levels of 60-70%. These conditions prevent premature curing and ensure proper gel formation during the dipping process.
The Manufacturing Process Step by Step
Pre-heating and Coagulant Application
The manufacturing cycle begins when clean formers enter pre-heat ovens where they’re heated to approximately 100°C. This temperature ensures optimal coagulant adhesion and prepares the former surface for latex application.
Heated formers then dip into the coagulant solution for 5-10 seconds. The coagulant concentration and dip time directly affect the final glove thickness and quality. Proper coagulant application creates an even layer that will interact with the latex proteins during the subsequent dipping process.
Latex Dipping Process
The coagulated formers proceed to the latex dipping tank, where they’re immersed in the compounded latex for 10-15 seconds. During this critical phase, latex proteins coagulate on the former surface, building up the glove thickness. The dipping depth determines the cuff length, while immersion time affects overall thickness.
Latex temperature during dipping typically ranges from 50-60°C, with pH maintained between 10-11. These parameters ensure optimal gel formation and prevent premature vulcanization.
Leaching and Protein Removal
Following the initial dip, formers with wet latex films pass through hot water leaching tanks. This process removes excess proteins, residual chemicals, and water-soluble impurities that could cause allergic reactions in end users.
The leaching process typically involves two to three sequential hot water baths at temperatures between 60-70°C. Each leaching stage lasts 3-5 minutes, with gentle agitation to enhance protein extraction without damaging the forming glove film.
Vulcanization Process
Vulcanization is the chemical process that transforms the latex film into a durable, elastic glove. Formers carrying the leached latex films enter vulcanization ovens where they’re exposed to temperatures between 100-130°C for 15-25 minutes.
During vulcanization, sulfur cross-links form between polymer chains, creating the characteristic strength and elasticity of latex gloves. Temperature profiles must be carefully controlled to prevent over-curing, which can make gloves brittle, or under-curing, which results in poor mechanical properties.
Quality Assurance and Testing
Physical Property Testing
Quality control laboratories conduct comprehensive testing on finished gloves to ensure they meet international standards. Key physical tests include:
Tensile Strength Testing: Measures the maximum stress a glove can withstand before breaking. Medical-grade latex gloves typically require minimum tensile strength of 18 MPa.
Elongation at Break: Evaluates the glove’s ability to stretch without tearing, with standards requiring minimum 650% elongation.
Modulus Testing: Determines the force required to stretch gloves to specific extensions, indicating material consistency.
Barrier Protection Evaluation
Gloves undergo rigorous barrier testing to ensure they provide adequate protection against various substances:
Pinhole Testing: Every glove is tested for microscopic holes using electrical conductivity methods or water leak tests.
Chemical Permeation Testing: Specialized testing evaluates resistance to specific chemicals relevant to intended applications.
Biological Barrier Testing: Medical gloves must demonstrate effectiveness against viral penetration according to ASTM F1671 standards.
Biocompatibility Assessment
Medical-grade latex gloves require extensive biocompatibility testing to ensure user safety:
Protein Content Analysis: Measures extractable proteins that could trigger allergic reactions, with FDA guidelines requiring less than 50 μg/g for low-protein gloves.
Cytotoxicity Testing: Evaluates potential cellular damage from glove extracts.
Sensitization Studies: Long-term testing to identify potential allergic responses.
Advanced Latex Gloves Machine Technology
Automated Quality Control Systems
Modern latex glove manufacturing incorporates sophisticated automated inspection systems that enhance quality control while reducing labor costs. Vision-based inspection systems use high-resolution cameras and artificial intelligence to detect defects in real-time during production.
These systems can identify various defects including:
- Thickness variations
- Surface irregularities
- Contamination particles
- Incomplete stripping
- Former marks
Advanced systems achieve inspection rates exceeding 1,000 gloves per minute with defect detection accuracy above 95%.
Smart Manufacturing Integration
Industry 4.0 technologies are revolutionizing latex glove production through smart manufacturing integration. Internet of Things (IoT) sensors monitor critical process parameters throughout the production line, providing real-time data on:
- Temperature profiles in ovens
- Latex viscosity and pH levels
- Conveyor speeds and timing
- Chemical concentration levels
This data enables predictive maintenance, reducing unplanned downtime and optimizing production efficiency.
Energy Efficiency Improvements
Modern latex gloves machine designs incorporate energy recovery systems that significantly reduce operational costs. Heat recovery units capture waste heat from vulcanization ovens and redirect it to pre-heating processes or facility heating systems.
Variable frequency drives on conveyor motors and pumps adjust energy consumption based on production demands, resulting in 15-25% energy savings compared to traditional fixed-speed systems.
Production Optimization and Efficiency
Line Speed Optimization
Production line efficiency depends on optimizing conveyor speeds while maintaining quality standards. Typical production lines operate at speeds between 15-30 meters per minute, with actual rates depending on glove thickness requirements and curing times.
Speed optimization involves balancing multiple factors:
- Latex gel strength development time
- Vulcanization temperature profiles
- Leaching effectiveness
- Quality control inspection capabilities
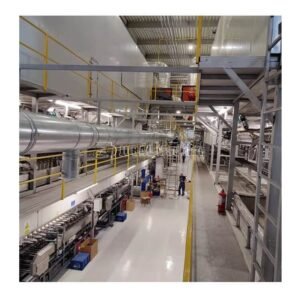
Yield Improvement Strategies
Manufacturers implement various strategies to maximize production yield and minimize waste:
Former Maintenance Programs: Regular cleaning and reconditioning of aluminum formers prevent defects and extend equipment life.
Latex Compound Optimization: Fine-tuning chemical formulations improves processability and reduces rejection rates.
Process Parameter Control: Statistical process control methods identify optimal operating windows for critical parameters.
Waste Reduction and Recycling
Sustainable manufacturing practices focus on minimizing waste generation and implementing recycling programs. Latex waste from trimming operations and rejected gloves can be reprocessed into various rubber products, reducing environmental impact and material costs.
Water treatment systems recover and recycle process water, reducing fresh water consumption and wastewater discharge volumes.
Environmental Considerations
Sustainable Raw Material Sourcing
Environmental responsibility in latex glove manufacturing begins with sustainable sourcing of natural rubber latex. Many manufacturers partner with certified plantations that follow responsible farming practices, including:
- Forest conservation programs
- Soil health management
- Worker welfare initiatives
- Biodiversity preservation
Emission Control Systems
Modern manufacturing facilities incorporate comprehensive emission control systems to minimize environmental impact. Air treatment systems capture and treat volatile organic compounds (VOCs) released during the vulcanization process.
Water treatment facilities process all wastewater before discharge, removing latex particles, chemical residues, and other contaminants to meet strict environmental regulations.
Life Cycle Assessment
Forward-thinking manufacturers conduct life cycle assessments to evaluate the complete environmental impact of their products from raw material extraction through disposal. These assessments guide decision-making on process improvements and material selections that reduce overall environmental footprint.
Conclusion
Latex glove manufacturing represents a complex integration of chemistry, engineering, and quality control systems. Success in this industry requires deep understanding of raw materials, precise process control, and commitment to continuous improvement.
The evolution toward smart manufacturing technologies and sustainable practices is reshaping the industry, offering opportunities for increased efficiency while reducing environmental impact. As global demand for latex gloves continues to grow, manufacturers who invest in advanced technologies and maintain rigorous quality standards will achieve long-term success.
Understanding these manufacturing principles provides the foundation for producing high-quality latex gloves that meet the demanding requirements of healthcare, food service, and industrial applications. The combination of traditional rubber chemistry knowledge with modern manufacturing technologies creates the optimal environment for successful latex glove production.