How Does a Latex Gloves Machine Work?
Table of Contents
- Introduction to Latex Gloves Machine
- Key Components of a Latex Gloves Machine
- The Latex Gloves Machine Manufacturing Process
- Types of Latex Gloves Machine Technology
- Quality Control in Latex Gloves Machine Operations
- Maintenance and Optimization of Latex Gloves Machine
- Future Innovations in Latex Gloves Machine Design
- Conclusion
Introduction to Latex Gloves Machine
The latex gloves machine represents one of the most sophisticated pieces of manufacturing equipment in the medical and industrial supply industry. These automated systems transform liquid latex into the disposable gloves that have become essential in healthcare, food service, and countless other industries. Understanding how a latex gloves machine operates provides insight into the complex engineering behind a product we often take for granted.
A modern latex gloves machine combines precision engineering with advanced automation to produce thousands of gloves per hour. The process involves multiple stages, from latex preparation to final packaging, all coordinated by sophisticated control systems that ensure consistent quality and efficiency.
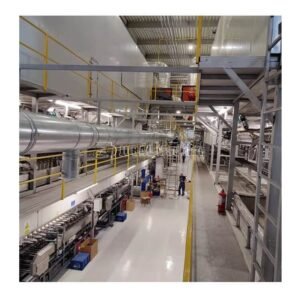
Key Components of a Latex Gloves Machine
Every latex gloves machine consists of several critical components that work in harmony to create the final product. The former line serves as the foundation of the operation, featuring hundreds of aluminum hand-shaped molds that rotate continuously through the production cycle. These formers are precisely engineered to create gloves of various sizes and specifications.
The coagulant tank represents another essential element of the latex gloves machine. This tank contains a calcium nitrate solution that causes the latex to coagulate when the formers are dipped into it. The concentration and temperature of this solution must be carefully controlled to ensure proper glove formation.
The latex compound tank holds the specially formulated latex mixture that will become the glove material. This tank maintains the latex at optimal temperature and viscosity while continuously agitating the mixture to prevent settling of additives and ensure uniform distribution of accelerators, sulfur, and other chemicals essential for vulcanization.
The Latex Gloves Machine Manufacturing Process
The operation of a latex gloves machine begins with the preparation phase, where clean formers enter a washing station to remove any residual materials from previous production cycles. The formers then pass through a drying oven to ensure they are completely moisture-free before entering the coagulant dipping station.
During the coagulant dipping phase, the latex gloves machine lowers the formers into the coagulant solution for a predetermined time, typically 10-15 seconds. The thickness of the eventual glove depends on the concentration of the coagulant and the dipping time. After coagulant application, the formers pass through another drying oven to remove excess moisture.
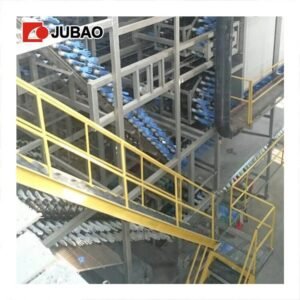
The latex dipping stage represents the heart of the latex gloves machine process. The coagulant-coated formers are immersed in the latex compound tank, where a thin layer of latex adheres to the former surface. The speed of withdrawal and the viscosity of the latex determine the final thickness of the glove. Some latex gloves machine configurations include multiple latex dipping stations to achieve desired thickness specifications.
Following latex application, the formers enter the vulcanizing oven, where temperatures reach 100-120°C. This heat treatment causes the sulfur in the latex to cross-link the rubber molecules, creating the elastic properties that make latex gloves functional. The vulcanization process typically takes 20-30 minutes, depending on the specific latex gloves machine configuration.
Types of Latex Gloves Machine Technology
Modern manufacturing facilities employ various types of latex gloves machine technology, each optimized for specific production requirements. Straight-line latex gloves machines feature a linear conveyor system that moves formers through each station in sequence. This design offers excellent accessibility for maintenance and quality control but requires more floor space.
Rotary latex gloves machines utilize a circular conveyor system that maximizes production capacity within a smaller footprint. These systems can accommodate more formers and often achieve higher production rates than straight-line configurations. The rotary design also allows for more efficient heat recovery systems, reducing energy consumption.
Some advanced latex gloves machine installations incorporate multi-line capabilities, where several parallel production lines share common latex preparation and curing systems. This approach maximizes equipment utilization and provides flexibility for producing different glove sizes or specifications simultaneously.
Quality Control in Latex Gloves Machine Operations
Quality control represents a critical aspect of latex gloves machine operations, as medical and food service applications demand consistently high standards. Automated inspection systems integrated into the latex gloves machine monitor glove thickness, detect pinholes, and identify surface defects in real-time.
The latex gloves machine incorporates various testing stations throughout the production line. Air inflation testing checks for pinholes and weak spots by inflating each glove and monitoring for pressure loss. Visual inspection systems use advanced cameras and lighting to detect color variations, foreign particles, and surface irregularities.
Statistical process control systems continuously monitor key parameters of the latex gloves machine operation, including latex viscosity, coagulant concentration, oven temperatures, and line speeds. These systems alert operators to deviations that could affect product quality and automatically adjust process parameters when possible.
Maintenance and Optimization of Latex Gloves Machine
Proper maintenance of a latex gloves machine is essential for consistent production and product quality. Daily maintenance routines include cleaning the formers, checking latex levels, and inspecting conveyor systems for wear. The former cleaning process is particularly critical, as any residue can cause defects in subsequent production runs.
Weekly maintenance of the latex gloves machine involves more thorough inspections of heating elements, temperature sensors, and mechanical components. The vulcanizing ovens require regular calibration to ensure uniform temperature distribution, while the latex circulation systems need cleaning to prevent contamination and maintain proper viscosity.
Preventive maintenance programs for latex gloves machines include scheduled replacement of wear parts, lubrication of moving components, and comprehensive system inspections. Modern latex gloves machine control systems provide predictive maintenance alerts based on operating hours, cycle counts, and performance trends.
Future Innovations in Latex Gloves Machine Design
The future of latex gloves machine technology focuses on increased automation, energy efficiency, and sustainability. Advanced sensor technologies are being integrated to provide real-time monitoring of latex properties, enabling automatic adjustment of process parameters to maintain optimal conditions.
Industry 4.0 principles are being applied to latex gloves machine operations, with interconnected systems that share data across the production line. This connectivity enables predictive maintenance, quality trend analysis, and production optimization that reduces waste and improves efficiency.
Environmental considerations are driving innovations in latex gloves machine design, including heat recovery systems that capture waste heat from vulcanizing ovens and water recycling systems that minimize environmental impact. Some manufacturers are developing latex gloves machines capable of processing bio-based latex alternatives to reduce dependence on natural rubber.
Conclusion
The latex gloves machine represents a remarkable achievement in manufacturing technology, combining precision engineering with automated control systems to produce essential protective equipment. From the initial coagulant dipping through final vulcanization, each stage of the process requires careful coordination and control to ensure consistent quality.
Understanding how a latex gloves machine works provides appreciation for the complexity behind a simple disposable glove. As technology continues to advance, these machines will become more efficient, sustainable, and capable of meeting the growing global demand for protective equipment. The integration of smart manufacturing principles and environmental consciousness will shape the next generation of latex gloves machine design, ensuring this critical technology continues to serve public health and safety needs worldwide.
More at: https://jubaomachine.com/new/glove-manufacturing-equipment/