How Does a Glove Dipping Machine Operate?
Table of Contents
- Understanding the Basic Principles of Glove Dipping Machine Operations
- Key Components of a Glove Dipping Machine System
- The Step-by-Step Glove Dipping Machine Process
- Types of Materials Used in Glove Dipping Machine Production
- Quality Control Measures in Glove Dipping Machine Operations
- Maintenance and Troubleshooting of Glove Dipping Machine Equipment
The manufacturing of disposable gloves has become increasingly important in healthcare, food service, and industrial applications. At the heart of this production process lies the sophisticated technology of glove dipping machines. These automated systems have revolutionized how protective gloves are manufactured, enabling mass production while maintaining consistent quality standards.
Understanding the Basic Principles of Glove Dipping Machine Operations
A glove dipping machine operates on the fundamental principle of coating hand-shaped forms, called formers, with liquid polymer materials to create protective gloves. The process begins with aluminum hand formers that are precisely shaped to match human hand dimensions. These formers are heated to optimal temperatures and then systematically dipped into tanks containing liquid latex, nitrile, or vinyl compounds.
The glove dipping machine utilizes a continuous conveyor system that moves the formers through various stations. Each station serves a specific purpose in the manufacturing process, from initial coating to final curing. The machine’s automation ensures consistent dipping depth, uniform coating thickness, and proper timing between each stage of production.
Temperature control plays a crucial role in glove dipping machine operations. The formers must maintain specific temperatures to ensure proper polymer adhesion and prevent defects. Modern machines incorporate advanced heating systems and temperature monitoring to maintain optimal conditions throughout the production cycle.
Key Components of a Glove Dipping Machine System
The glove dipping machine consists of several essential components that work together to produce high-quality gloves. The former carrier system represents the backbone of the operation, featuring chains or belts that transport the aluminum hand formers through the entire production line. These carriers are designed to handle hundreds or thousands of formers simultaneously, depending on the machine’s capacity.
Dipping tanks constitute another critical component of the glove dipping machine. These stainless steel vessels contain the liquid polymer materials and are equipped with agitation systems to maintain consistent mixture properties. The tanks feature precise level controls and filtration systems to remove impurities that could affect glove quality.
The heating and curing ovens integrated into the glove dipping machine system provide the necessary thermal energy to vulcanize or cure the polymer coating. These ovens utilize hot air circulation, infrared heating, or steam systems to achieve the required temperatures for proper glove formation. Advanced temperature profiling ensures uniform heat distribution across all formers.
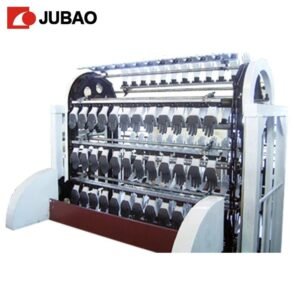
The Step-by-Step Glove Dipping Machine Process
The glove dipping machine process begins with former preparation, where clean aluminum hand formers are heated to approximately 60-80°C. This preheating stage ensures optimal polymer adhesion and prevents the formation of air bubbles or weak spots in the final product.
During the initial dipping phase, the heated formers are lowered into the first polymer tank at a controlled speed. The glove dipping machine maintains precise dipping depth and withdrawal rates to achieve uniform wall thickness. The dwell time in the polymer solution is carefully controlled to ensure complete coating coverage.
Following the initial dip, the formers pass through a gel-curing oven where the polymer begins to solidify. This stage in the glove dipping machine process is critical for developing the glove’s basic structure and strength. The temperature and duration of this curing phase directly impact the final product’s mechanical properties.
A second dipping stage may occur in some glove dipping machine configurations, particularly for thicker gloves or specialized applications. This additional coating layer enhances durability and provides extra protection. The machine’s control systems coordinate the timing and positioning of formers throughout this multi-stage process.
The final curing stage involves passing the coated formers through high-temperature ovens where complete vulcanization occurs. The glove dipping machine maintains precise temperature profiles to ensure thorough curing without degrading the polymer structure. This step determines the glove’s final strength, elasticity, and chemical resistance properties.
Types of Materials Used in Glove Dipping Machine Production
Modern glove dipping machines are designed to handle various polymer materials, each requiring specific processing parameters. Natural rubber latex remains a popular choice due to its excellent elasticity and barrier properties. The glove dipping machine must maintain latex compound stability through controlled temperature and pH levels throughout the production process.
Nitrile rubber compounds have gained significant popularity in glove dipping machine applications due to their superior chemical resistance and reduced allergy potential. These synthetic materials require precise temperature control and may need longer curing times compared to natural latex. The machine’s heating systems must accommodate these requirements while maintaining production efficiency.
Vinyl compounds represent another material category processed by glove dipping machines. These PVC-based materials offer cost-effective solutions for many applications but require specialized handling due to their thermoplastic nature. The glove dipping machine must maintain lower processing temperatures to prevent material degradation.
Quality Control Measures in Glove Dipping Machine Operations
Quality assurance in glove dipping machine operations involves multiple monitoring and testing procedures. Continuous thickness measurement systems integrated into the machine track wall thickness variations and automatically adjust processing parameters to maintain specifications. These real-time monitoring capabilities ensure consistent product quality throughout production runs.
The glove dipping machine incorporates defect detection systems that identify common issues such as pinholes, thin spots, or contamination. Advanced optical inspection systems can detect microscopic defects that might compromise glove integrity. Automated rejection systems remove defective products from the production line without interrupting the manufacturing process.
Regular calibration and maintenance of the glove dipping machine components ensure accurate temperature control, proper timing sequences, and consistent polymer application. Preventive maintenance schedules help identify potential issues before they affect product quality or cause production disruptions.
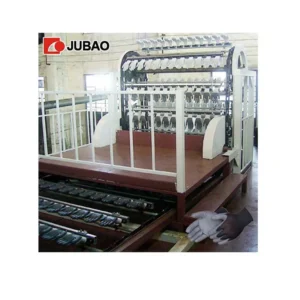
Maintenance and Troubleshooting of Glove Dipping Machine Equipment
Proper maintenance of glove dipping machine systems is essential for consistent production and equipment longevity. Daily maintenance routines include cleaning polymer tanks, checking heating element functionality, and inspecting former carriers for wear or damage. Regular cleaning prevents polymer buildup that could affect product quality or machine performance.
The glove dipping machine’s mechanical components require periodic lubrication and alignment checks. Chain tensioning, bearing inspection, and drive system maintenance ensure smooth operation and prevent unexpected breakdowns. Scheduled maintenance intervals help maintain optimal machine performance and extend equipment life.
Troubleshooting common glove dipping machine issues requires understanding the relationship between processing parameters and product quality. Temperature fluctuations, polymer contamination, or timing irregularities can all affect glove properties. Systematic diagnostic procedures help identify root causes and implement corrective actions quickly.
Modern glove dipping machines incorporate sophisticated control systems that log operational data and alert operators to potential issues. These monitoring systems track key performance indicators and can predict maintenance needs before problems occur. Proper training of maintenance personnel ensures effective troubleshooting and minimal production disruptions.
The evolution of glove dipping machine technology continues to improve efficiency, product quality, and operational flexibility. Understanding these complex systems enables manufacturers to optimize their production processes and meet the growing demand for high-quality protective gloves across various industries.
More at: Glove machine seires